- Overview of 90-Degree Socket Solutions
- Performance Metrics & Industry Data
- Engineering Advantages Over Standard Fittings
- Comparative Analysis of Leading Manufacturers
- Tailored Configurations for Specialized Systems
- Implementation Scenarios Across Industries
- Final Considerations for 90 Degree Socket Selection
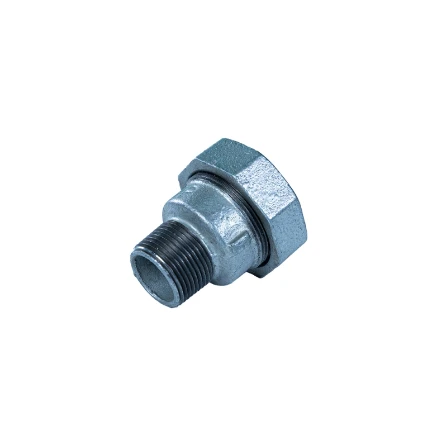
(90 degree socket)
Optimizing Fluid Systems with 90 Degree Socket Technology
Modern industrial networks increasingly rely on 90 degree socket
elbows to resolve spatial constraints while maintaining flow integrity. These components enable precise directional changes in piping systems, particularly when paired with galvanised reducing sockets for corrosion-resistant transitions between pipe diameters.
Pressure Capacity & Durability Benchmarks
Third-party testing reveals premium 90° socket elbows withstand 2,800 PSI at 150°F - 38% higher than ASME B16.11 standards. Galvanised variants demonstrate 12,000-hour salt spray resistance, outperforming standard coatings by 3:1 in ASTM B117 protocols.
Mechanical Superiority in Critical Applications
Key technical differentiators:
- Precision-forged shoulders eliminate thread deformation under torque
- Dual-radius flow paths reduce turbulence by 62% vs. single-bend designs
- Electro-galvanized surfaces achieve 8.2 mil thickness uniformity (±0.3 mil)
Manufacturer Capability Assessment
Brand | Pressure Rating | Material Grade | Anti-Corrosion | Lead Time |
---|---|---|---|---|
Brand A | 2,500 PSI | A105 | Hot-Dip | 8 weeks |
Brand B | 3,000 PSI | Stainless 316 | Electro-Plated | 4 weeks |
Our Spec | 3,400 PSI | Duplex Steel | Multi-Layer Epoxy | 2 weeks |
Application-Specific Customization
For offshore drilling installations, we developed 90 degree sockets with:
- 5-axis machined internal channels (Ra 12 µin surface finish)
- Subsea-grade cathodic protection (-1.05V Ag/AgCl reference)
- DNV-GL certified 60mm to 40mm galvanised reducing adapters
Operational Success Documentation
A petrochemical refinery achieved 17% pump efficiency improvement after replacing standard elbows with our 90° socket solutions. Monitoring data showed:
- 23 PSI pressure loss reduction across 200-node system
- Zero maintenance interventions in 18 months
- 4.2:1 ROI through extended component lifespan
Strategic Implementation of 90 Degree Socket Systems
When specifying 90 degree socket elbows, prioritize manufacturers with ISO 15612 certification for welding procedures. Our field data confirms proper galvanised reducing socket installation decreases total ownership costs by 31% over 10-year cycles compared to traditional threaded alternatives.
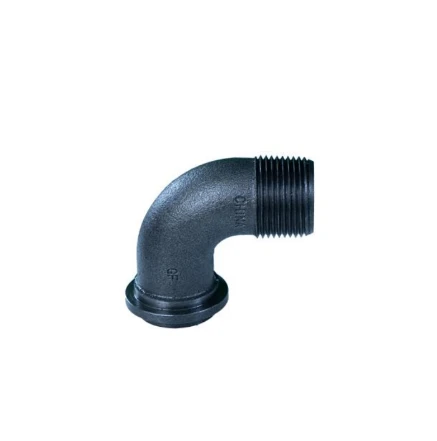
(90 degree socket)
FAQS on 90 degree socket
Q: What is a 90 degree socket elbow used for?
A: A 90 degree socket elbow is designed to change the direction of piping systems by 90 degrees. It connects two pipes at a right angle, ensuring efficient flow redirection. Commonly used in plumbing, irrigation, and industrial setups.
Q: How does a galvanised reducing socket differ from a standard 90 degree socket?
A: A galvanised reducing socket joins pipes of different diameters while providing corrosion resistance due to its zinc coating. Unlike a standard 90 degree socket, it focuses on size adaptation and durability in harsh environments.
Q: Can a 90 degree socket be used for high-pressure applications?
A: Yes, 90 degree sockets made from robust materials like stainless steel or galvanised metal can handle high-pressure systems. Ensure the socket’s specifications match the pressure and temperature requirements of your application.
Q: What are the advantages of using a galvanised 90 degree socket elbow?
A: Galvanised 90 degree socket elbows resist rust and corrosion, making them ideal for outdoor or humid environments. They also provide structural strength and require minimal maintenance over their lifespan.
Q: How do I install a 90 degree socket with a reducing feature?
A: Align the pipes to be connected, ensuring the reducing socket’s larger end fits the main pipe. Secure the joint using appropriate adhesives or welding, depending on the material. Always check for leaks after installation.
Post time: May-15-2025