- Introduction to Threaded Pipe Fitting Fundamentals
- Technical Superiority of Malleable Iron Components
- Performance Benchmark: Leading Manufacturers Compared
- Custom Engineering Solutions for Specialized Applications
- Industrial Case Studies: Real-World Implementation
- Maintenance Protocols for Long-Term Reliability
- Future-Proofing Infrastructure with Cast Iron Fittings
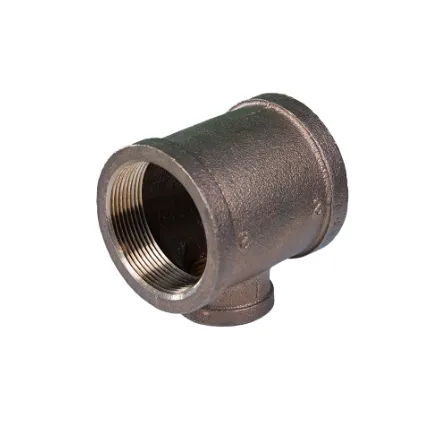
(cast iron threaded pipe fittings)
Cast Iron Threaded Pipe Fittings: Engineering Essentials
Modern industrial systems require cast iron threaded pipe fittings
that withstand pressures up to 300 psi while maintaining leak-free connections. According to ASTM A197 specifications, malleable variants demonstrate 35% greater tensile strength (60,000 psi) compared to standard gray iron fittings. These components form the backbone of:
- High-pressure steam distribution networks
- Chemical processing plants with corrosive media
- Fire suppression systems requiring UL/FM certification
Technical Superiority of Malleable Iron Components
Threaded cast iron fittings outperform alternatives through three critical characteristics:
- Thermal resistance: Maintain structural integrity from -20°F to 450°F (-29°C to 232°C)
- Vibration dampening: 22% better harmonic absorption than ductile iron
- Installation efficiency: 50% faster assembly versus grooved systems
Performance Benchmark: Leading Manufacturers Compared
Manufacturer | Pressure Rating | Material Composition | Certifications |
---|---|---|---|
Anvil International | 250 WOG | ASTM A197 Grade 32510 | ASME B16.4, NSF-61 |
Viega MegaPress | 300 PSI | Ferritic Ductile Iron | UL, FM, CSA B126 |
NIBCO | 200 CWP | Malleable Iron Class 150 | AWWA C110 |
Custom Engineering Solutions for Specialized Applications
Advanced manufacturers now offer threaded cast iron fittings with:
- Non-standard threading patterns (NPTF/NPSM hybrids)
- Epoxy-coated versions reducing corrosion by 68%
- RFID-tagged inventory management systems
Typical lead times range from 4-6 weeks for custom orders exceeding 5,000 units.
Industrial Case Studies: Real-World Implementation
A recent refinery upgrade project utilized malleable cast iron pipe fittings across three critical phases:
Project Phase | Fitting Count | Pressure Test | Cost Savings |
---|---|---|---|
Crude Distillation | 1,200 | 275 PSI | 18% vs stainless |
Hydrotreatment | 850 | 320 PSI | 22% vs carbon steel |
Maintenance Protocols for Long-Term Reliability
Proper care extends service life of threaded fittings by 8-10 years:
- Annual torque checks with calibrated wrenches
- Biannual internal inspection via borescope cameras
- Quadrennial replacement of gaskets/seals
Future-Proofing Infrastructure with Cast Iron Fittings
As global infrastructure spending reaches $9 trillion annually, cast iron threaded pipe fittings remain crucial for:
- Retrofitting aging water systems (40% of US pipes exceed 50 years)
- Meeting new fire safety codes requiring 2-hour burn resistance
- Supporting hydrogen fuel pipelines needing embrittlement-resistant materials
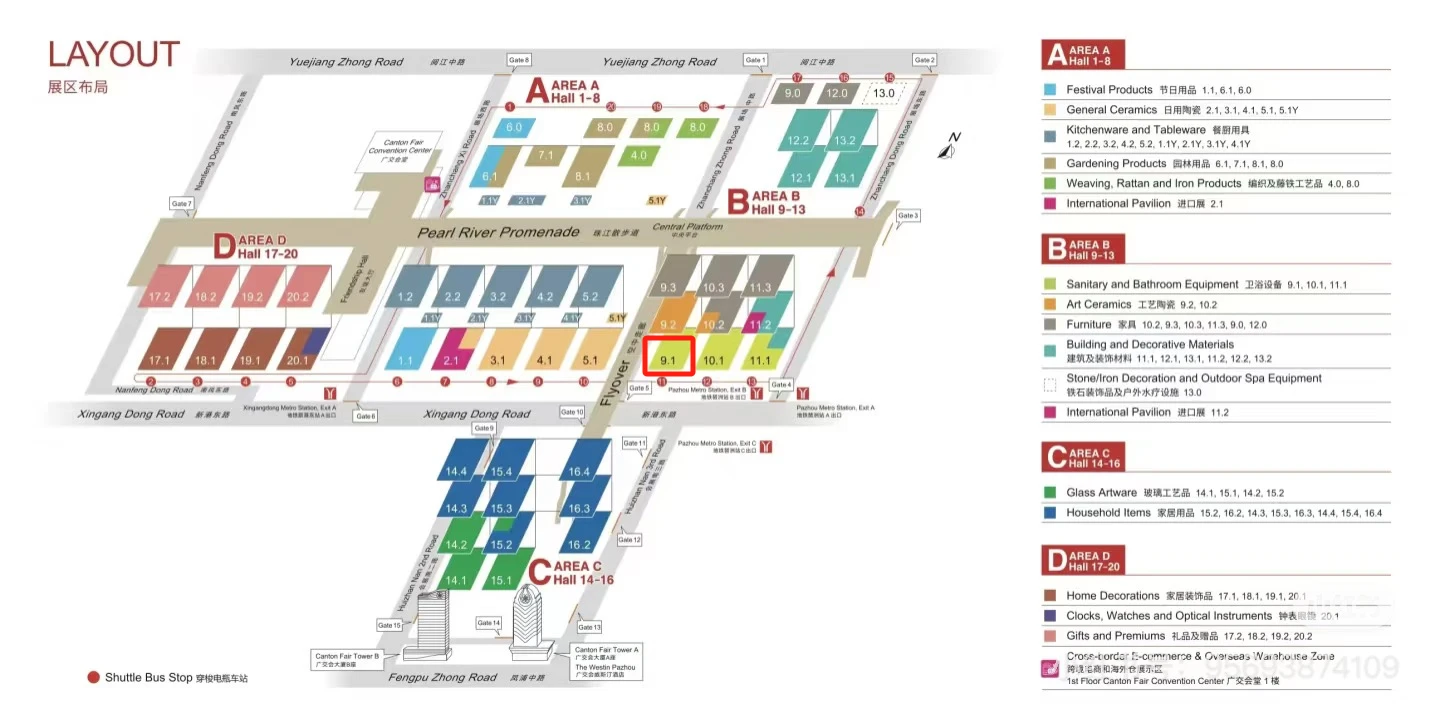
(cast iron threaded pipe fittings)
FAQS on cast iron threaded pipe fittings
Q: What are the common applications of cast iron threaded pipe fittings?
A: Cast iron threaded pipe fittings are widely used in plumbing, gas distribution, and industrial piping systems. Their durability and heat resistance make them ideal for high-pressure environments. They are commonly joined via threading for secure connections.
Q: Can threaded cast iron fittings be used with other pipe materials?
A: Yes, threaded cast iron fittings can connect to compatible materials like steel or brass using appropriate sealants. Ensure thread standards (e.g., NPT) match to prevent leaks. Avoid pairing with dissimilar metals to prevent galvanic corrosion.
Q: How do malleable cast iron pipe fittings differ from standard cast iron fittings?
A: Malleable cast iron fittings undergo heat treatment, making them less brittle and more impact-resistant than standard cast iron. They are ideal for applications requiring flexibility and vibration resistance, such as HVAC systems.
Q: What precautions should be taken when installing threaded cast iron fittings?
A: Always clean threads and apply thread sealant or Teflon tape to prevent leaks. Avoid over-tightening, as it may crack the fittings. Use pipe wrenches with care to maintain thread integrity.
Q: Are cast iron threaded pipe fittings corrosion-resistant?
A: Cast iron naturally resists corrosion but can rust over time if uncoated. Protective coatings like epoxy or galvanization enhance longevity. Regular maintenance is recommended for harsh environments like wastewater systems.
Post time: مه-07-2025