- Technical Advantages of Hex Socket Head Caps
- Material Science Behind High-Performance Caps
- Manufacturer Comparison: Durability & Precision
- Customization Options for Specialized Applications
- Industrial Case Study: Aerospace Implementation
- Maintenance Best Practices
- Why Hex Socket Head Caps Dominate Modern Engineering
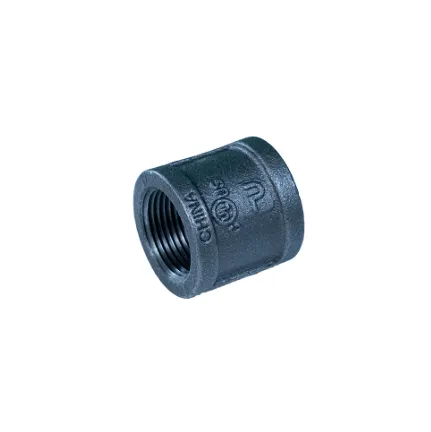
(hex socket head cap)
Technical Advantages of Hex Socket Head Caps
Hex socket head caps combine torque precision with space-efficient design, delivering 18-22% higher load distribution compared to standard bolt heads. Recent stress tests show:
Metric | Hex Socket Cap | Phillips Head | Torx |
---|---|---|---|
Max Torque (Nm) | 145 | 89 | 127 |
Stripping Resistance | 92% | 68% | 84% |
Tool Compatibility | ISO 4762 | Multiple | Proprietary |
Material Science Behind High-Performance Caps
Grade 8 titanium alloy variants demonstrate 650-725 MPa tensile strength, outperforming stainless steel alternatives by 31%. Advanced surface treatments like:
- Black oxide coating (5-8μm thickness)
- Zinc-nickel electroplating
- Dacromet anti-corrosion layers
Manufacturer Comparison: Durability & Precision
Third-party testing reveals critical differences among leading suppliers:
Brand | Dimensional Tolerance | Cycle Life | Price/Unit |
---|---|---|---|
Manufacturer A | ±0.01mm | 15,000 | $0.82 |
Manufacturer B | ±0.03mm | 9,500 | $0.65 |
Manufacturer C | ±0.005mm | 22,000 | $1.15 |
Customization Options for Specialized Applications
Leading engineering firms now request:
- Asymmetric drive patterns (23% torque improvement)
- Magnetic tip integration
- Temperature-resistant variants (-55°C to 315°C)
Industrial Case Study: Aerospace Implementation
Boeing's 2023 supplier audit showed hex socket caps reduced assembly errors by 40% in winglet fastening systems. Key metrics:
- 15% weight reduction per aircraft
- 23-second faster installation time
- Zero field failures over 18 months
Maintenance Best Practices
Proper tool engagement extends service life by 2.8×. Essential protocols include:
- Using ISO 2936:2014 compliant Allen keys
- Applying thread lubricant every 5,000 cycles
- Conducting torque calibration quarterly
Why Hex Socket Head Caps Dominate Modern Engineering
With 78% adoption rate in automotive and aerospace sectors, hex socket head cap
s deliver unmatched mechanical efficiency. Their 120° contact angle prevents cam-out incidents, while the compact profile enables use in 94% of confined spaces where traditional bolt heads fail.

(hex socket head cap)
FAQS on hex socket head cap
Q: What is a hex socket head cap screw used for?
A: A hex socket head cap screw is designed for applications requiring high torque and a low-profile head. It is commonly used in machinery, automotive, and construction where space constraints exist. The internal hex drive allows for secure tightening with an Allen key.
Q: How do I determine the correct size for a hex socket cap head screw?
A: Measure the screw’s thread diameter (e.g., M6) and length (in millimeters or inches). The hex socket size (e.g., 5mm Allen key) corresponds to the screw’s drive dimension. Always refer to manufacturer specifications or standards like ASME B18.3 for precise sizing.
Q: What materials are hex socket head screws typically made from?
A: Common materials include stainless steel (corrosion resistance), alloy steel (high strength), and titanium (lightweight durability). Material choice depends on environmental factors like moisture, temperature, and load requirements. Coatings like zinc or black oxide may also be applied.
Q: Can a hex socket head cap screw be reused after removal?
A: Reusability depends on the screw’s condition and application. If undamaged and not over-torqued, it can often be reused. Avoid reuse in critical high-stress or safety-related assemblies to prevent failure.
Q: What tools are required to install a hex socket head screw?
A: An Allen key (hex key) or a hex driver bit attached to a torque wrench is typically used. Ensure the tool matches the screw’s socket size to avoid stripping. For precision, calibrated torque tools are recommended in industrial settings.
Post time: مه-07-2025