Flexible couplings are indispensable components in the field of mechanical engineering, serving as crucial intermediaries that enhance the transmission of power between shafts while accommodating unavoidable misalignments. As industries evolve with technology, the need for durable and efficient flexible couplings has never been more paramount. This article sheds light on the expertise and experience embedded in choosing the right flexible coupling for industrial applications, emphasizing authoritative insights that bolster trust.
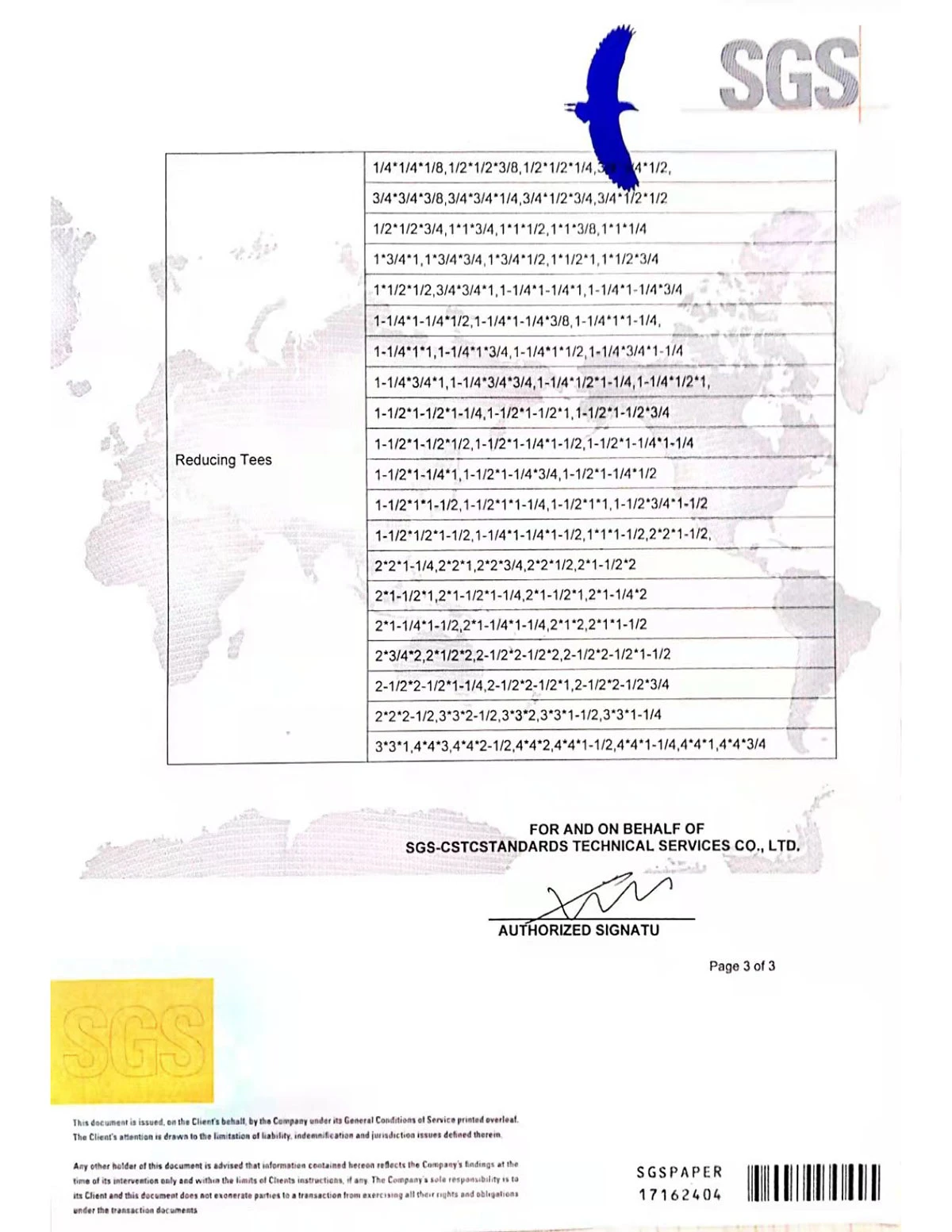
Central to the utility of flexible couplings is their ability to absorb misalignments between connected shafts. Whether in manufacturing equipment, automobiles, or heavy machinery, these devices manage axial, radial, and angular discrepancies that, if unchecked, could lead to significant operational downtimes and increased maintenance costs. The nuanced engineering behind flexible couplings allows them to accept a degree of misalignment while maintaining performance consistency—a testament to their ingenuity.
There are various types of flexible couplings, each designed to address specific kinds of misalignment and load conditions. For instance, elastomeric couplings, often made from rubber or other polymeric materials, are prized for their vibration damping properties. They are an excellent choice for applications where noise reduction and vibration isolation are priorities. Meanwhile, metallic couplings, often favored for high-torque applications, offer superior strength and durability, making them ideal for heavy-duty machinery subjected to variable loads.
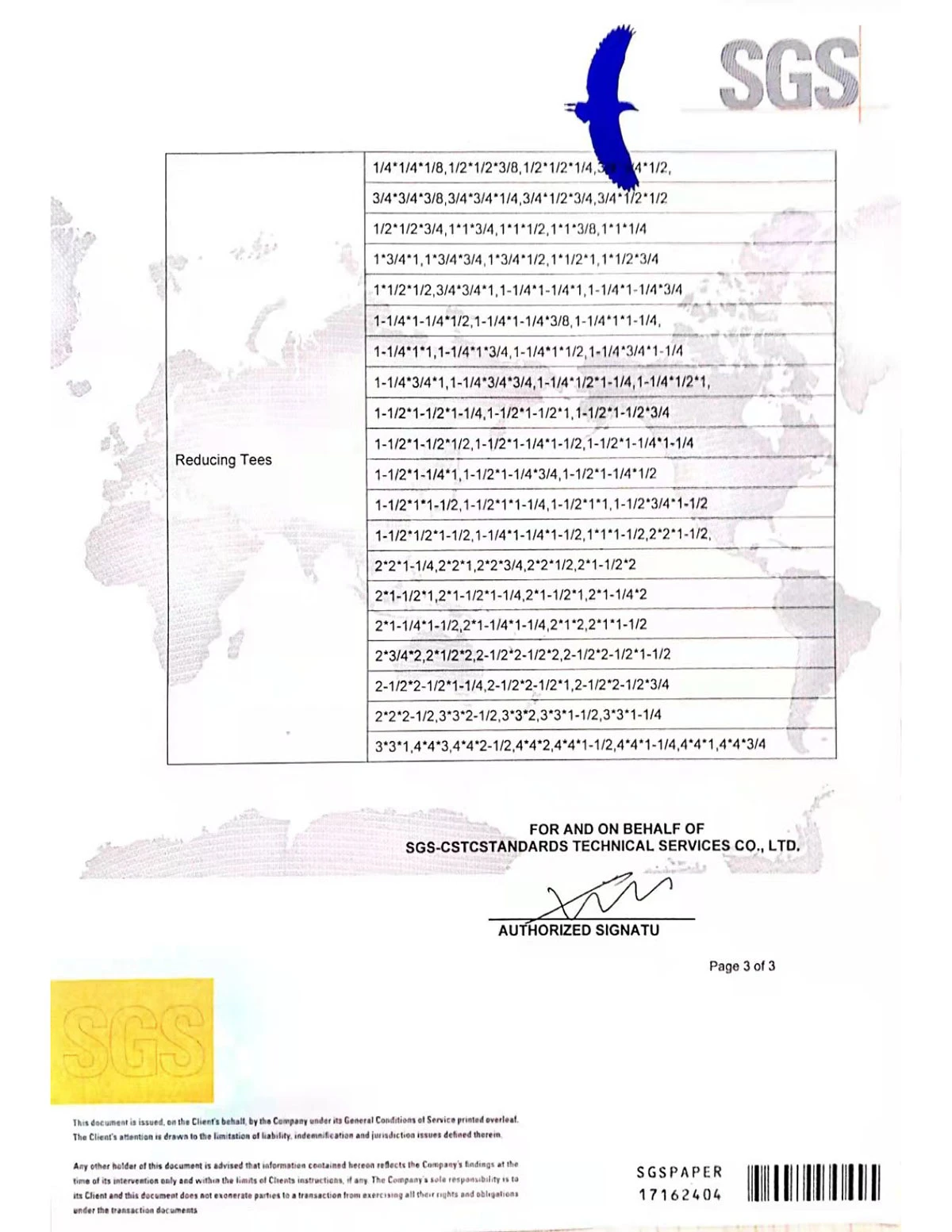
In the quest for enhanced reliability, certain innovations in flexible coupling design have emerged. The incorporation of composite materials has led to couplings that offer superior strength-to-weight ratios, enhancing operational efficiency by reducing inertial losses. Furthermore, the advent of precision engineering and 3D printing has allowed for custom coupling designs that can be tailored for specific industrial needs, offering unparalleled precision and reduced lead times.
Selecting the right flexible coupling demands a keen understanding of the operational environment and load conditions. Engineers and procurement specialists must consider factors such as torque requirements, speed ranges, shaft sizes, and environmental conditions like temperature and humidity. It is paramount to consult with reputable suppliers and manufacturers who offer not only a range of products but also extensive technical support and consultation services.
The credibility and authority of the supplier play a critical role in ensuring that the selected coupling will deliver optimal performance over its intended lifetime.
flexible coupling
Moreover, industry standards such as ISO and ASTM offer guidelines that can guide professionals in making informed decisions. Compliance with these standards ensures the coupling meets specified safety and performance benchmarks, further cementing trust in their application. It is advisable to prioritize products that adhere to these industry benchmarks, as they have undergone rigorous testing to validate their efficacy and reliability.
Testimonials and case studies from industries that have successfully integrated flexible couplings can also offer valuable insights. These real-world examples illuminate the coupling's capabilities and adaptability, showcasing scenarios where they have significantly reduced maintenance downtimes and enhanced machine efficiency. Experiences from sectors such as aerospace, automotive, and industrial manufacturing can provide an empirical basis for assessing the coupling's performance under diverse operational conditions.
Ultimately, the decision-making process surrounding flexible couplings must weigh both current operational needs and future scalability. As industries strive towards automation and digital transformation, the ability of a coupling to integrate with advanced monitoring systems and predictive maintenance tools is becoming increasingly important. Couplings that support smart diagnostics can facilitate the early detection of misalignments and wear, minimizing unplanned maintenance and extending the equipment's lifespan.
In conclusion, flexible couplings are critical components that offer both performance enhancements and protection to mechanical systems. Their ability to accommodate misalignments, absorb vibrations, and adapt to various loads underscores their indispensable role in modern machinery. By leveraging newfound innovations and industry standards, and by considering the comprehensive expertise offered by trusted manufacturers, industries can ensure optimal coupling performance, thus safeguarding and prolonging the lifespan of their equipment. This measured approach not only mitigates risks but also enhances operational efficiency, ultimately contributing to the sustainable success of industrial operations.
Post time:
Gen-20-2025