The art of connecting pipes of varying diameters is a challenge ubiquitous in plumbing and mechanical systems. Traditionally, fittings serve the purpose of bridging these differences, ensuring a seamless flow without compromising the system's integrity. An essential component in this mechanism is the reducer fitting,
strategically designed to connect two different pipe sizes together.

Reducer fittings come in various types, such as concentric and eccentric reducers, each serving unique purposes in fluid dynamics. A concentric reducer has a cone-shaped, symmetrical design. This symmetry allows it to mitigate turbulence in the flow, ideal for vertical piping systems where equal pressure distribution is crucial. Conversely, eccentric reducers are more suited for horizontal piping, designed to maintain the same top or bottom level of each pipe to avoid accumulation of gases or solids.
Engineering and material selection play pivotal roles. Expertise in metallurgy and polymer science can guide the choice between stainless steel, PVC, or brass reducers, depending on the fluid type, operating pressure, and environmental conditions. For fluid systems subjected to aggressive chemicals or high temperatures, stainless steel reducers offer unparalleled durability and resistance. Conversely, PVC reducers are lightweight, cost-effective, and perfect for low-pressure systems.
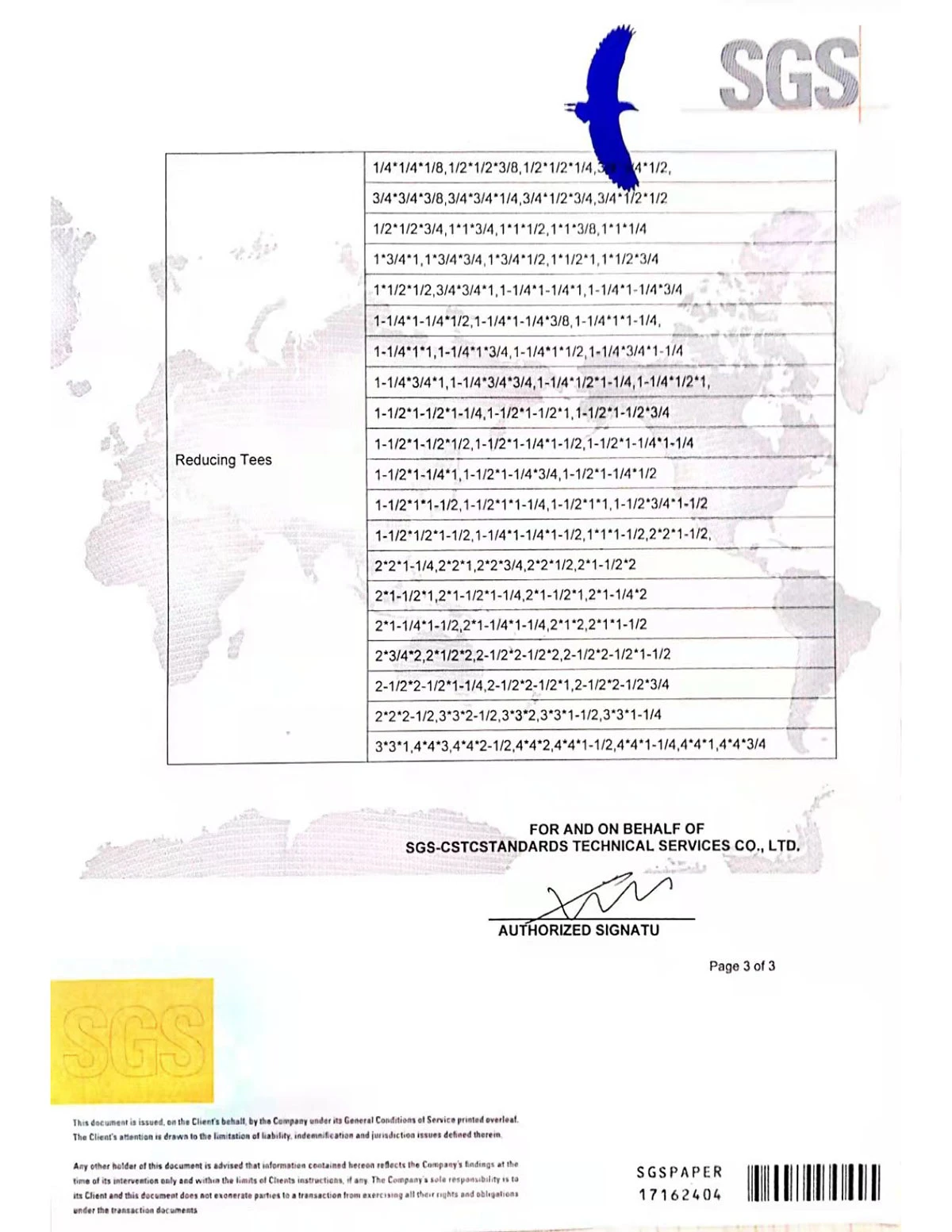
Real-world experiences often dictate the optimal usage scenarios for these fittings. Case studies in industrial plumbing systems illustrate how improper selection or installation of reducers leads to inefficiencies, such as pressure loss, increased energy consumption, and even catastrophic leaks. Therefore, experience in assessing system requirements and pressure considerations is non-negotiable for ensuring seamless operations.
From a maintenance perspective, the trustworthiness of reducer fittings is paramount. Reliability is guaranteed through rigorous testing and certification by authoritative bodies like the American Society for Testing and Materials (ASTM). Consistent standards ensure each fitting adheres to precise specifications, providing peace of mind for engineers and maintenance crews alike.
a fitting used to connect two different pipe sizes together
The economic impact of using appropriate reducer fittings cannot be overlooked. Investing in high-quality, well-designed fittings translates to reduced downtime and maintenance costs. In industrial settings, where every operational minute counts, this equates to increased profitability and sustainability over the long haul.
Innovations in smart manufacturing have introduced reducers equipped with sensors, providing real-time data on flow rates and pressure differentials. This technological advancement aids in predictive maintenance, allowing operators to preemptively address issues before they escalate into costly repairs or interruptions.
To ensure proper implementation, collaboration with seasoned suppliers is crucial. They bring a wealth of knowledge and expertise, from advising on the best fittings for specific applications to training teams on installation and maintenance practices that safeguard system integrity.
In summary, the successful connection of varying pipe sizes using reducer fittings is an intricate dance of material science, engineering expertise, and experiential learning. As systems become more complex and demand greater efficiency and reliability, the role of these fittings becomes even more critical. Comprehensive understanding and careful application of reducer fittings not only enhance operational efficiency but also secure their status as indispensable components in modern infrastructure.
Post time:
1月-10-2025