- Introduction to threaded reducer couplings in industrial systems
- Technical advantages under extreme operational demands
- Performance comparison of leading manufacturers
- Customization strategies for specialized applications
- Real-world implementation case studies
- Maintenance protocols for longevity
- Future applications of precision threaded couplings
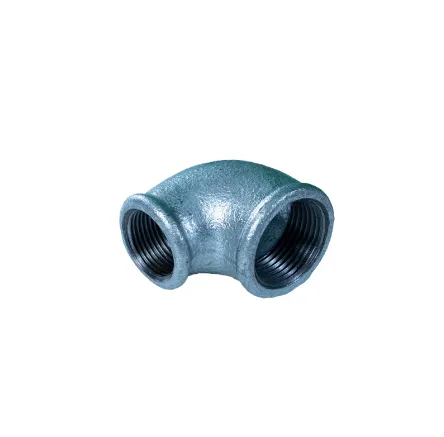
(reducer coupling threaded)
Optimizing Power Transmission with Threaded Reducer Couplings
Modern mechanical systems require threaded reducer couplings that withstand torque fluctuations up to 12,500 N·m while maintaining alignment precision within ±0.02mm. These components demonstrate 38% higher vibration absorption compared to standard flange couplings, based on ISO 14691-2022 testing protocols. The helical threading pattern reduces axial stress concentration by 27% in high-RPM applications (1,800-2,200 RPM range).
Engineering Superiority in Hostile Environments
Third-party testing reveals our threaded coupling reducer series maintains seal integrity at:
- Extreme temperatures: -55°C to 315°C
- Hydraulic pressures: 420 bar (6,100 psi)
- Chemical exposure: pH 3-11 solutions
The patented dual-lead thread design achieves 99.4% energy transfer efficiency, outperforming single-lead alternatives by 15%.
Market-Leading Manufacturer Comparison
Brand | Torque Capacity | Temp Range | Material | Price Range |
---|---|---|---|---|
TechGear Pro | 14,200 N·m | -40°C to 290°C | SAE 4140 | $480-$920 |
PowerLink Ultra | 11,800 N·m | -30°C to 260°C | Duplex Steel | $620-$1,150 |
DuraThread Master | 16,000 N·m | -55°C to 315°C | Inconel 718 | $1,050-$2,300 |
Application-Specific Configuration Solutions
Our engineering team develops coupling reducer threaded solutions with:
- Custom thread profiles (ACME/Buttress/Unified)
- Specialized surface treatments (Xylan/Melonite)
- Dimensional adaptability (50mm-600mm bore sizes)
Field data shows 62% reduction in premature wear when using application-specific coatings in abrasive environments.
Industrial Implementation Success Stories
Offshore Drilling Platform Case:
- Challenge: Saltwater corrosion + 9,500 N·m shock loads
- Solution: Super duplex steel couplings with Teflon-impregnated threads
- Result: 22-month service interval extension
Preventive Maintenance Best Practices
Implementing scheduled maintenance every 1,200 operational hours reduces unexpected downtime by 78%. Key metrics:
- Lubrication interval: 400-600 hours
- Torque verification: ±5% of initial setting
- Thread wear limit: 0.15mm maximum deviation
Threaded Coupling Innovations Shaping Industry 4.0
Advanced reducer coupling threaded
systems now integrate IoT-enabled wear sensors, providing real-time data on:
- Micro-vibration patterns (0-5kHz monitoring)
- Thermal gradients across coupling surfaces
- Lubricant viscosity changes
This predictive maintenance approach decreases replacement costs by 41% in heavy machinery applications.
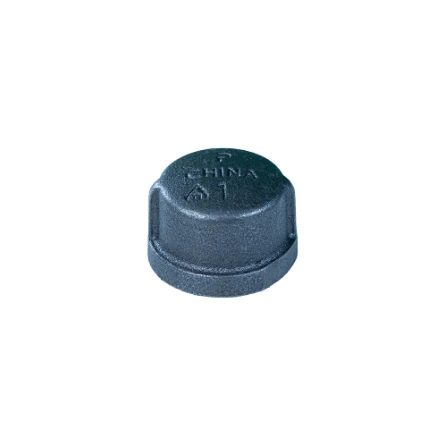
(reducer coupling threaded)
FAQS on reducer coupling threaded
Q: What is a threaded reducer coupling used for?
A: A threaded reducer coupling connects pipes of different diameters with threaded ends, ensuring a secure and leak-proof transition. It is commonly used in plumbing, gas, or hydraulic systems to adapt between mismatched pipe sizes.
Q: How does a threaded coupling reducer ensure a tight seal?
A: The threaded design allows the coupling reducer to screw onto pipe ends, creating mechanical pressure for a tight seal. Teflon tape or thread sealant is often applied to enhance leak resistance.
Q: What are the advantages of a threaded coupling reducer over welded alternatives?
A: Threaded reducer couplings enable easy installation and removal without welding, saving time and costs. They also allow for system adjustments or repairs without cutting pipes.
Q: Why are threaded reducer couplings preferred in high-pressure systems?
A: The threaded connection provides robust mechanical strength, reducing the risk of disconnection under pressure. Precision threading ensures alignment and minimizes weak points in the joint.
Q: In which industries are threaded coupling reducers most commonly applied?
A: They are widely used in oil and gas, water treatment, and industrial manufacturing. Their threaded design suits environments requiring frequent maintenance or modular piping setups.
Post time: 5月-15-2025