In the intricate world of piping systems, the 180 degree elbow holds a distinctive position. Often overshadowed by its more commonly discussed counterparts, such as the 90 and 45 degree elbows, this particular type of bend plays an essential, if somewhat specialized, role in industrial applications and home installations alike. Delving deeper into its applications and advantages, one gains a clear appreciation of its importance.
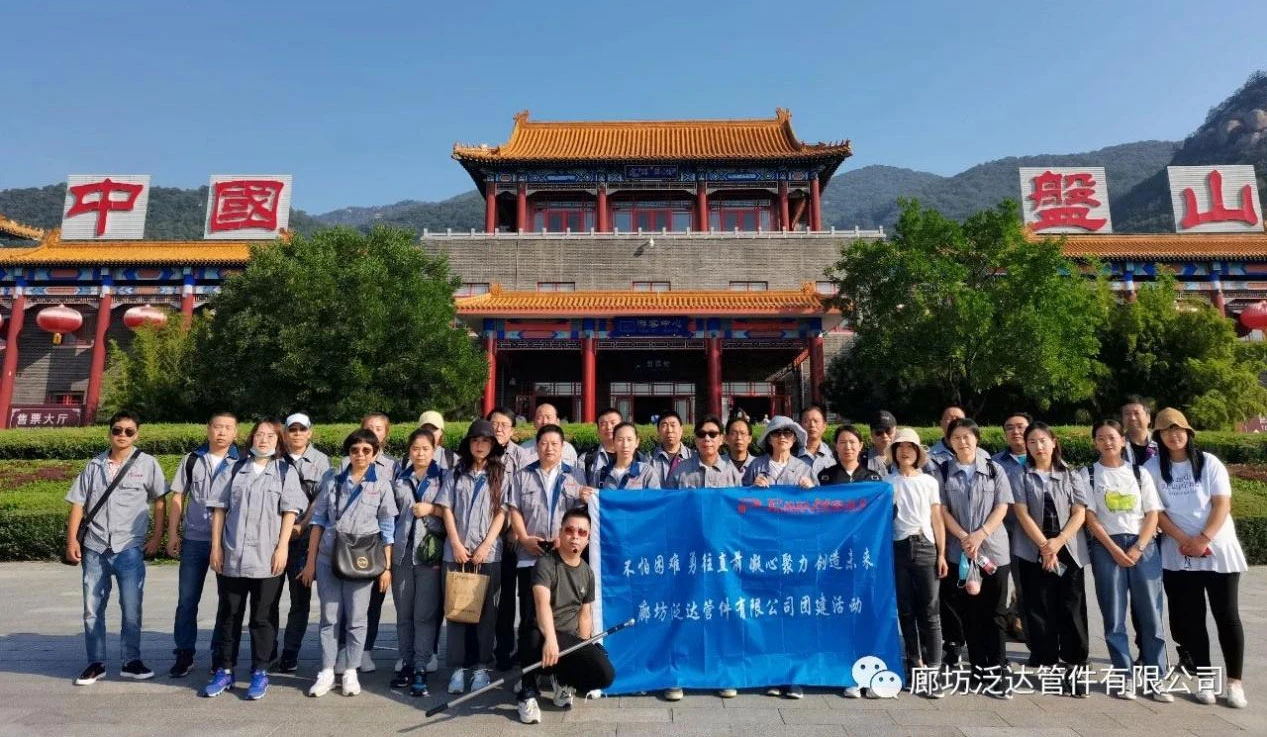
A 180 degree elbow is, essentially, a conduit fitting allowing a pipe to make a full directional turnaround. Unlike other elbows that change the fluid flow direction at an angle,
the 180-degree version reverses it completely. This capability makes it indispensable in situations requiring a compact design, where space constraints are significant. The design and application of 180 degree elbows are backed by engineering expertise based on fluid dynamics principles, ensuring minimal pressure drop and turbulence which might otherwise be a concern.
Specialty industries such as petrochemical, pharmaceutical, and power generation demand precise systems where even minor disruptions can lead to major inefficiencies. In these contexts, the seamless integration of a 180 degree elbow becomes imperative. For instance, petrochemical complexes, characterized by endless networks of pipes carrying various fluids at high temperatures and pressures, depend on the reliable performance of these elbows to maintain system integrity and operational efficiency.
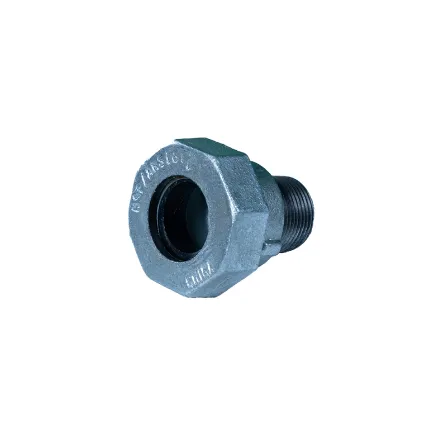
Additionally, crafting a 180 degree elbow demands a high degree of manufacturing prowess. The choice of material is critical, particularly when employed in harsh environments. Stainless steel, cast iron, and high-strength alloys are common due to their durability and resistance to corrosion. Each material offers distinct advantages stainless steel is renowned for its resilience against rusting, cast iron provides heft and robustness, and specialized alloys deliver tailored resistance to extreme temperatures or chemical reactions.
With the continued emphasis on efficiency and sustainability, the demand for high-performance 180 degree elbows grows. Engineers and system designers trust their expert knowledge and experience to select the right elbow, accounting for flow characteristics and thermal profiles. One must consider the quality of fabrication, compliance to industry standards like ANSI and ASME, and certification that guarantees optimal performance.
180 degree elbow
Moreover, extensive research and development further bolster the credibility and reliability of these components. Research facilities experimenting with flow models and pressure systems provide empirical data that push these designs to new heights, enhancing their robustness and efficiency.
Of course, trust in the adoption of 180 degree elbows is built not just on product specs and industry standards. Word-of-mouth from seasoned professionals who have experienced their reliability firsthand cements their place in many applications. Testimonials from industry experts highlight scenarios where these fittings have performed flawlessly under duress, thereby ensuring operational continuity and safety.
Lastly, an essential component in embracing the full utility of 180 degree elbows is regular maintenance. Routine inspections help identify welding defects or potential weaknesses that might compromise efficiency. In environments where wear and tear are inevitable, regular checking ensures longevity and sustained performance of the entire piping system.
In conclusion, while seemingly straightforward, the 180 degree elbow is a vital piece of engineering that underscores the intricate balance of functionality and efficiency in pipe systems across the globe. Its specialized role, garnered through proven expertise and enduring trust, highlights its value in applications where every component matters. Leveraging this knowledge, industry professionals can ensure robust, efficient, and safe pipeline designs, maximizing both the performance and lifespan of their systems.
Post time:
Fev-15-2025