Understanding the complexities of mechanical systems often requires a deep dive into the components that enable seamless operation. One such vital component, often overlooked,
is the reducer coupling, particularly the 112 to 12 reducer coupling. For industry professionals and hobbyists alike, this device is more than just a connector; it is a pivotal element in ensuring mechanical efficiency and precision.
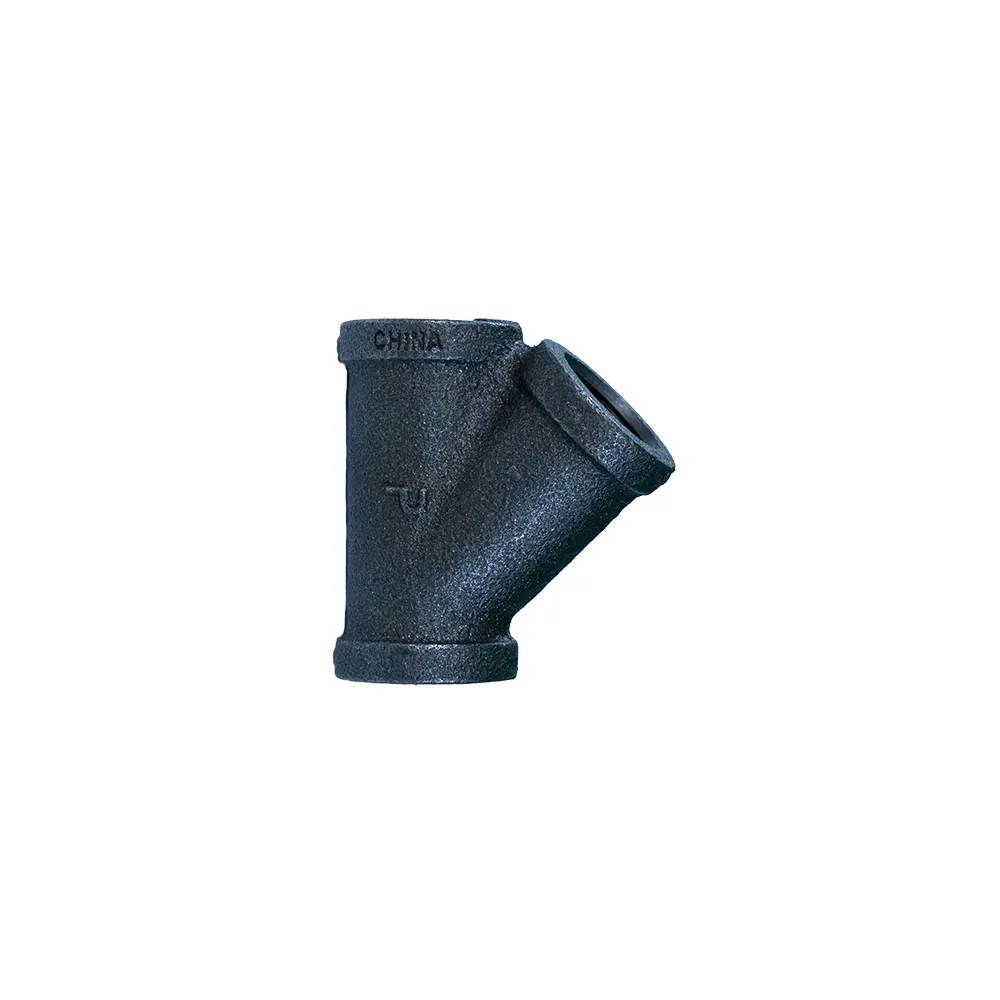
Reducer couplings are critical in applications requiring torque and speed adjustments between shafts in machinery. The specific 112 to 12 ratio is designed to balance speed and power in mechanical systems, supporting a variety of applications from industrial machinery to specialized equipment.
Experience with using the 112 to 12 reducer coupling showcases its unique ability to solve common issues faced with direct shaft connection, such as misalignment and vibration, leading to reduced wear and tear. Imagine an automated conveyor system where precise speed control and alignment are paramount; a poorly fitted connection could lead to frequent downtime and maintenance. However, implementing a 112 to 12 reducer coupling can significantly mitigate these issues by providing greater flexibility and control in system alignment.
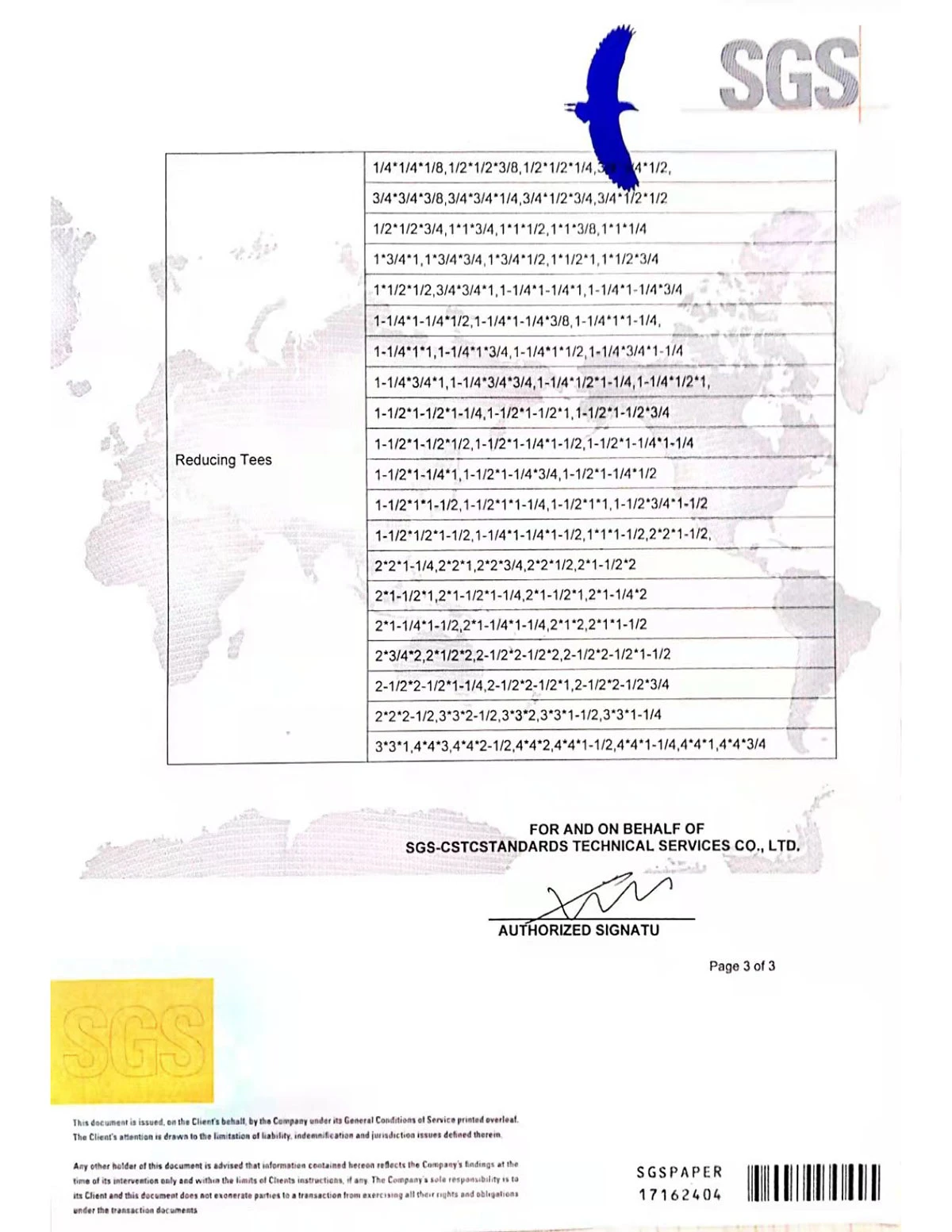
From an expertise standpoint, understanding the mechanics behind the reducer coupling can enhance its implementation in various fields, such as robotics, automotive, and manufacturing. The genius of the 112 to 12 ratio lies in its ability to facilitate the specific torque-to-speed conversions needed for different mechanical applications. With its precise design, it allows engineers to customize machine outputs without extensive overhauls, making it a cost-effective solution in engineering projects.
Authoritativeness in the field often comes from both academic and practical insights into the components that ensure machine efficiency. An authoritative perspective on the 112 to 12 reducer coupling would highlight how its unique gearing proportion aids in achieving desired operational outputs without compromising structural integrity or increasing costs disproportionately. Experts recommend considering these couplings because they offer seamless power transmission capabilities while accommodating potential misalignment between connected shafts.
1 1 2 to 1 2 reducer coupling
For large-scale applications, trustworthiness in component performance is non-negotiable. The reliability of the 112 to 12 reducer coupling is often verified through rigorous testing and compliance with industry standards. By consistently demonstrating durability and efficiency, these couplings have become a trusted choice for engineers looking to optimize their mechanical designs. For instance, in an energy plant where turbines require consistent torque and alignment, the use of a high-quality reducer coupling can lead to fewer mechanical failures, ensuring uninterrupted power generation.
Professionals working with reducer couplings should also be aware of material choices and their implications on performance. Typically constructed from durable metals such as steel or aluminum, the coupling must withstand environmental stresses and operational demands. This includes understanding the coupling’s load capacity, potential exposure to heat or chemicals, and its lifespan under continuous usage.
In the world of mechanical design and function, staying ahead necessitates a continuous learning curve and adaptation to best practices. Encouraging deeper research into the efficiency gains and challenges involving reducer couplings can lead to more innovative applications and enhancements in machine designs. The 112 to 12 reducer coupling stands out as a pivotal element in this pursuit, allowing for tailored solutions that address specific operational hurdles.
Ultimately, being informed and judicious in selecting and utilizing components like the 112 to 12 reducer coupling can lead to significant advantages in performance and longevity of machinery. For engineers and operational managers, it's about aligning practical needs with mechanical realities, ensuring that the systems they design and maintain meet both current and future demands.
This streamlined approach not only supports immediate operational needs but also lays the foundation for advancements in mechanical systems, paving the way for innovations that can redefine their applications across industries.
Post time:
Фев-11-2025