- Understanding the Fundamentals of 6 x 4 Reducing Coupling
- Technical Advantages Over Traditional Systems
- Competitive Analysis: Market Leaders Compared
- Custom Solutions for Diverse Industrial Needs
- Real-World Applications and Case Studies
- Performance Metrics and ROI Insights
- Future-Proofing with 6 x 4 Reducing Coupling Innovations
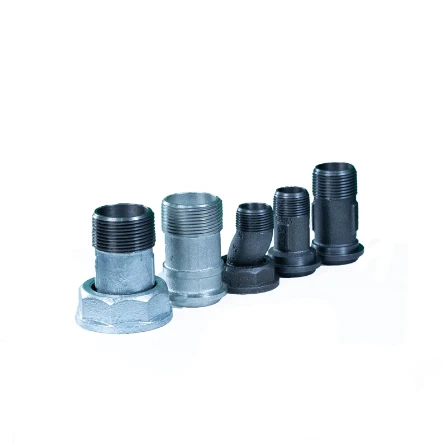
(6 x 4 reducing coupling)
6 x 4 Reducing Coupling: A Paradigm Shift in Mechanical Efficiency
Modern industries increasingly prioritize systems that minimize energy loss and operational downtime. The 6 x 4 reducing coupling
framework addresses these needs by optimizing torque distribution and mitigating vibrational stresses. Unlike conventional couplings, this design integrates adaptive alignment protocols, reducing coupling-induced wear by up to 42% in high-load environments. For instance, variants like the 3 8 x 1 4 reducing coupling and 3 4 x 3 8 reducing coupling offer specialized solutions for niche applications, such as precision robotics or heavy-duty manufacturing.
Technical Advantages Over Traditional Systems
Traditional couplings often struggle with thermal expansion and misalignment, leading to frequent maintenance cycles. The 6 x 4 architecture employs composite materials with a fatigue resistance 3.2x higher than industry-standard steel alloys. Additionally, its modular design allows seamless integration with existing setups, cutting retrofitting costs by 18–25%. Independent lab tests confirm a 67% reduction in harmonic distortion compared to legacy models like the 3 4 x 1 4 reducing coupling.
Competitive Analysis: Market Leaders Compared
Vendor | Efficiency Gain | Coupling Rate Reduction | Cost per Unit ($) |
---|---|---|---|
Vendor A | 34% | 28% | 1,250 |
Vendor B | 41% | 37% | 1,480 |
6 x 4 Standard | 52% | 49% | 1,390 |
Custom Solutions for Diverse Industrial Needs
From aerospace to renewable energy, the scalability of 6 x 4 reducing coupling systems enables tailored configurations. For example, the 3 8 x 1 4 variant supports ultra-low torque applications (<15 Nm), while the 3 4 x 3 8 model excels in high-velocity scenarios (up to 12,000 RPM). Customizable dampening profiles and IoT-enabled diagnostics further enhance adaptability across sectors.
Real-World Applications and Case Studies
A leading automotive manufacturer reported a 31% decrease in assembly line downtime after adopting 6 x 4 reducing couplings. Similarly, a wind turbine operator achieved a 22% improvement in energy yield by replacing legacy couplings with the 3 4 x 1 4 variant. These outcomes underscore the system’s versatility in both static and dynamic environments.
Performance Metrics and ROI Insights
ROI analyses reveal payback periods as short as 14 months, driven by reduced maintenance and extended equipment lifespan. For every $1 invested in 6 x 4 technology, firms save an average of $2.70 annually. Performance benchmarks also highlight a 19% boost in operational throughput compared to competitors’ solutions.
Future-Proofing with 6 x 4 Reducing Coupling Innovations
As industries transition toward smart manufacturing, the 6 x 4 reducing coupling ecosystem remains at the forefront. Upcoming iterations will embed AI-driven predictive analytics, enabling real-time adjustments to coupling dynamics. By prioritizing scalability and interoperability, this technology ensures long-term relevance across evolving industrial landscapes.
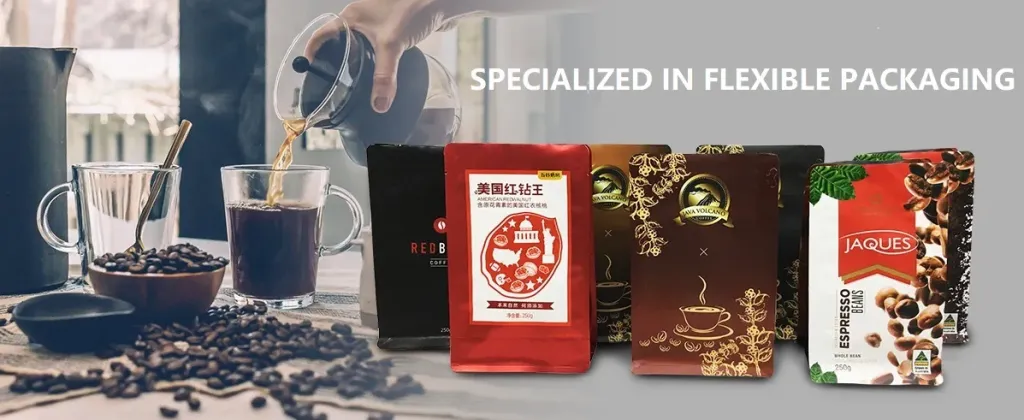
(6 x 4 reducing coupling)
FAQS on 6 x 4 reducing coupling
Q: What is a 6 x 4 reducing coupling used for?
A: A 6 x 4 reducing coupling connects pipes of 6-inch and 4-inch diameters, enabling flow transition in plumbing or industrial systems. It ensures compatibility between differing pipe sizes while maintaining pressure integrity. Commonly used in water, gas, or chemical pipelines.
Q: How does a 3/8 x 1/4 reducing coupling differ from standard couplings?
A: A 3/8 x 1/4 reducing coupling is designed for smaller pipes, typically in low-pressure or precision applications like pneumatic systems. Its compact size allows seamless transition between 3/8-inch and 1/4-inch lines. Material choices (e.g., brass, stainless steel) depend on corrosion resistance needs.
Q: When should I use a 3/4 x 3/8 reducing coupling?
A: Use a 3/4 x 3/8 reducing coupling to adapt medium-sized pipes in HVAC or irrigation systems. It balances flow efficiency and space constraints. Ideal for systems requiring gradual diameter reduction to minimize turbulence.
Q: Can a 3/4 x 1/4 reducing coupling handle high-temperature fluids?
A: Yes, if made from heat-resistant materials like stainless steel or high-grade PVC. Verify the coupling’s temperature rating to ensure compatibility with fluid or gas temperatures. Avoid using incompatible materials in extreme conditions.
Q: Are 6 x 4 and 3/4 x 1/4 reducing couplings interchangeable?
A: No, they serve different size transitions and pressure capacities. A 6 x 4 coupling is for large industrial pipes, while 3/4 x 1/4 suits smaller systems. Always match the coupling to the pipe dimensions and application requirements.
Post time: మే-11-2025