In the intricate world of plumbing, HVAC, and various industrial applications, the 90-degree bend stands as an unsung hero. This simple yet essential component plays a pivotal role in directing flow, ensuring functionality, and optimizing space. When selecting the right 90-degree bend, understanding its applications, materials, and performance characteristics is imperative for achieving optimal results.
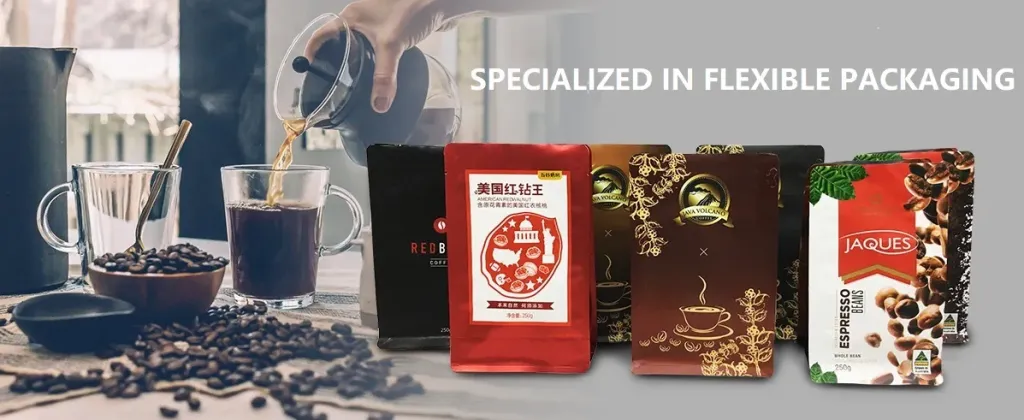
For those unfamiliar, a 90-degree bend is essentially a pipe fitting used to change the direction of flow in a piping system. Its presence is ubiquitous across industries including construction, automotive, aerospace, and domestic plumbing systems. The ability to seamlessly alter the path of liquid, gas, or other materials is crucial, especially when navigating tight spaces or complex layouts.
Experience in practical applications reveals that the selection process for a 90-degree bend is multifaceted. First and foremost, one must assess the material compatibility. Common materials for these fittings include stainless steel, copper, PVC, and aluminum. Each material offers distinct advantages—stainless steel boasts resistance to corrosion and heat, making it ideal for high-pressure and high-temperature environments, while PVC is economical and lightweight, suitable for low-pressure applications.
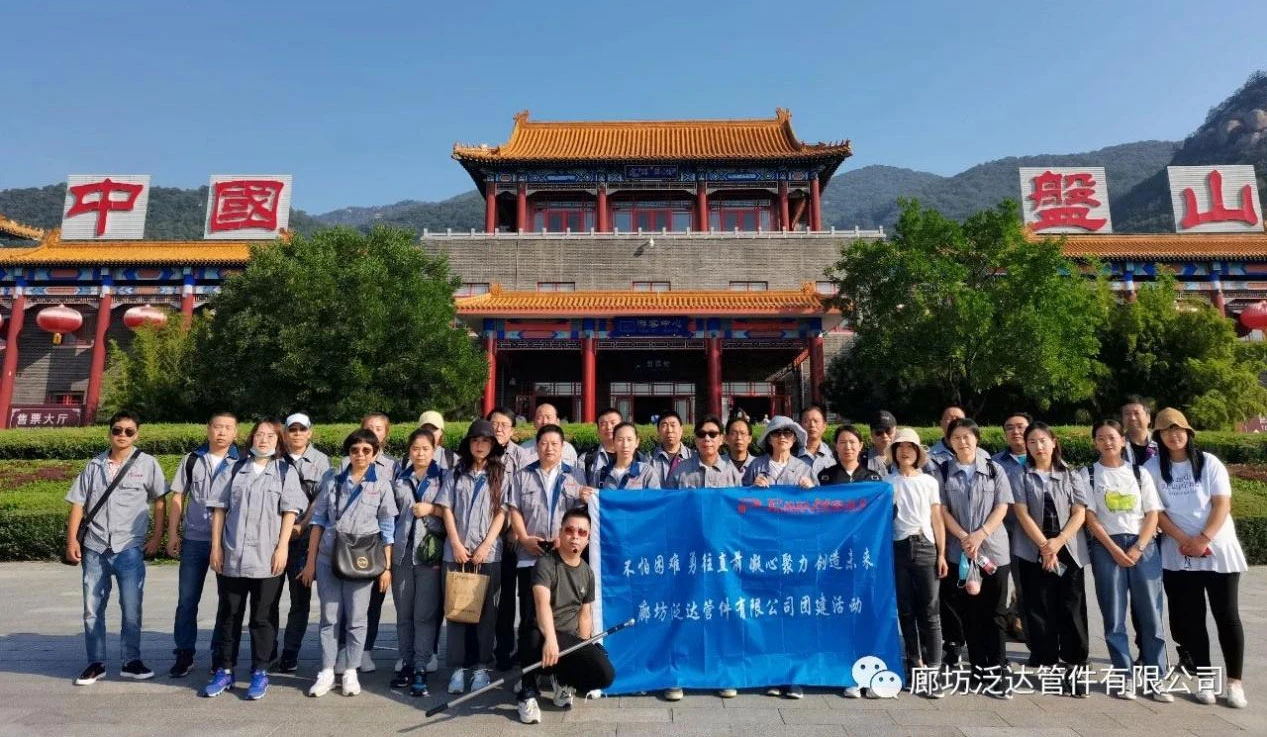
When evaluating expertise, engineers consider the inner diameter, wall thickness, and radius of the bend. These factors determine the bend's ability to withstand pressure and prevent cavitation—a phenomenon where vapor bubbles form in a liquid due to rapid changes in pressure, potentially causing damage. Precision in these specifications is critical in industries where safety and reliability cannot be compromised.
Authoritativeness in this domain is often represented by compliance with recognized standards and certifications. For instance, ISO (International Organization for Standardization) and ANSI (American National Standards Institute) provide guidelines ensuring fittings meet essential safety and performance criteria. Utilizing fittings that align with these standards ensures they have passed rigorous testing, thereby guaranteeing quality and durability.
90 degree bend
Trustworthiness in a supplier is paramount—choosing a reputable manufacturer with a track record of reliability can prevent costly failures and downtime. Transparent sourcing of materials, consistent production processes, and customer support are some of the hallmarks of a trustworthy provider. Continuous product innovation and customer feedback integration further reinforce the reliability of a brand's offerings.
In practical terms, the right 90-degree bend can enhance the efficiency of a system by minimizing friction loss—a crucial consideration in fluid dynamics. The smoother the flow, the less energy required, which can translate to significant cost savings over time. Moreover, careful installation and maintenance are vital, as improperly aligned or fitted bends can result in leaks or obstruction, affecting entire systems.
For those in the market for 90-degree bends, evaluating long-term value over upfront costs is crucial. High-quality bends not only ensure longevity and performance but also contribute to sustainable operations by reducing the need for frequent replacements and repairs. In sectors where time equals money, ensuring systems run smoothly with minimal interruption can drastically improve bottom lines.
In conclusion, the 90-degree bend may appear modest, but its significance is profound in the vast landscape of industry and construction. Through meticulous selection and strategic application, this component serves as a cornerstone for efficient and effective system design. Emphasizing experience, expertise, authoritativeness, and trustworthiness in its procurement and utilization can lead to enhanced performance, safety, and cost-efficiency across diverse applications.
Post time:
1 月-14-2025