Connecting two pipes of different diameters is essential in various plumbing, industrial, and irrigation applications. Selecting the right fitting for this particular task is crucial to ensure efficiency, safety, and durability of the piping system.
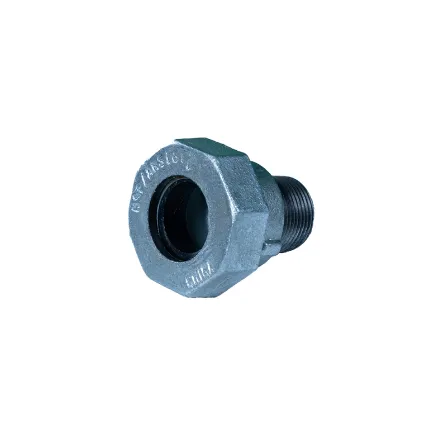
First and foremost, understanding the material compatibility is vital. Pipes made from materials like PVC, copper, steel, or PEX each have unique properties and react differently under pressure. For instance, PVC is suitable for cold-water systems due to its high resistance to corrosion, while copper is the choice for hot water because of its high thermal conductivity and durability. Each material may require specialized fittings; therefore, knowledge about the piping material is imperative.
Choosing an appropriate fitting type is the next step. Common connectors include reducers, bushings, and couplings. Reducers are used to connect two pipes of different diameters in a straightforward manner, often shaped like a cone or funnel. On the other hand, bushings allow changing the diameter within the same fitting, effectively decreasing or increasing the pipe’s bore size. Couplings, though typically used for pipes of the same diameter, can sometimes accommodate bushings to fit smaller pipes.
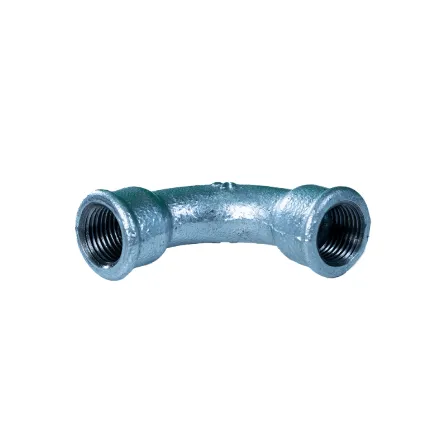
Once you have identified the fitting type needed, the method of connection is the next consideration. Mechanical joints, such as threaded or flanged connections, and push-fit solutions offer flexibility and ease of installation. Threaded joints are commonly found in metal pipes, providing a strong, leak-proof seal when correctly installed. Push-fit fittings are gaining popularity for their versatility in connecting dissimilar materials without the need for solvents or welding, ensuring a quick and reliable installation.
The environment in which the piping is installed can affect the choice of fittings. Outdoor applications, for example, demand fittings resistant to ultraviolet rays and temperature fluctuations. Under such conditions, brass and stainless steel fittings offer excellent resistance to corrosion and external weather conditions. For indoor installations, cost-effectiveness might dictate the use of alternatives like cast iron or PVC, provided they meet the operational pressure requirements.
Precision in measurements cannot be overstated. Ensuring the accurate diameter of both pipes is critical in selecting the correct fitting. A slight miscalculation can lead to leaks or even system failures, causing potential financial and environmental damage. Professional measurement tools like vernier calipers or pipe gauges can facilitate precise readings, preventing costly errors in diameter mismatch.
fitting to connect 2 diameter pipe
When efficiency and reliability are paramount, considering the flow velocity between the two pipes is essential. An abrupt change in pipe size can create turbulence, potentially impacting flow rates and system pressure. Gradual reducers tend to alleviate such issues by providing a smoother transition for the flow, maintaining consistent pressure and minimizing wear on the system components.
Professionals must also be aware of the operational pressure the piping system will encounter. Fittings come in varying pressure ratings; thus, matching these with the system’s maximum pressure ensures longevity and safety. A fitting rated for lower pressure than required can fail, risking both personal safety and structural integrity.
Proper sealing is indispensable in ensuring the fitting’s efficacy. For threaded connections, the utilization of PTFE tape or pipe dope can prevent leaks while facilitating a secure joint. Compression fittings often employ rubber grommets or rings, which must be regularly checked for wear and replaced when necessary to maintain sealing integrity.
The choice between solvent welding, soldering, or mechanical fittings often reflects a balance between cost and operational requirements. Solvent welding creates a sturdy, seamless joint used predominantly with PVC; soldering is preferred with copper due to its high-pressure and temperature resilience; mechanical fittings offer installation ease and are adaptable to a variety of materials.
After successfully connecting pipes with different diameters, regular maintenance checks are vital to ensure continued performance. Inspections can preemptively identify minor issues before they escalate, safeguarding both property and equipment.
For the optimal performance and longevity of your piping system, engage with experienced professionals or suppliers who possess in-depth knowledge of materials, fitting types, and industry standards. Leveraging authoritative resources not only enhances the credibility of the system but also builds trust with stakeholders and clients. Bringing expertise into every stage of selecting and installing pipe fittings ensures a seamless and efficient piping network adaptable to future changes and expansions.
Post time:
Jan-25-2025