In the ever-evolving industrial landscape, one product category consistently in demand is mechanical reducers, especially those involving coupling and threading technology. The demand for end-use efficiency drives many industries to constantly seek innovative solutions, and reducer coupling threaded systems play a vital role in this evolution. By exploring the nuances of these systems, we provide a comprehensive guide on how these components elevate industrial functioning.
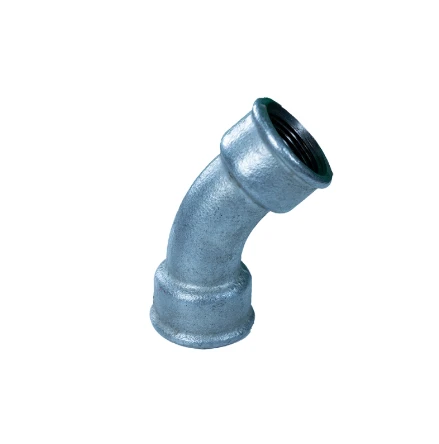
Reducer coupling threaded systems, designed to connect shafts of different diameters in various machines, are an engineering marvel. Their primary purpose is to transfer torque while also compensating for potential misalignment. The threaded aspect of these coupling reducers ensures precise engagement, making it possible to fine-tune connections to the desired tension and alignment. This precision is crucial in maintaining the integrity of mechanical systems over time.
One of the defining experiences with threaded reducer couplings is their versatile application across numerous sectors, ranging from heavy machinery manufacturing to precision engineering industries. These sectors rely heavily on machinery performance, which directly translates to productivity and, by extension, profitability. The deployment of high-quality reducer coupling threaded components can significantly ameliorate issues related to mechanical wear-and-tear, subsequently offering longevity and reliability.

From an expertise standpoint, the design and material selection for these components are pivotal. Advancements in metallurgy have led to the production of reducers using high-grade stainless steel, carbon alloy, and other composites, ensuring both durability and resistance to environmental challenges such as corrosion. Experienced engineers understand the importance of these materials in providing resilience and maintaining functionality under strenuous conditions. Customized threading allows for enhanced torque transfer, vital for achieving optimal performance.
Industry experts acknowledge that the authoritative value of a reducer coupling threaded system lies in its precision engineering and customization capability. With increased emphasis on sustainability, manufacturers are tailoring reducers to not only meet but exceed industry standards for energy efficiency and reduced emissions. The precision fitting of threaded couplers minimizes energy loss, ensuring that machinery runs at peak efficiency while consuming less power. This is an essential consideration for industries looking to reduce their carbon footprint.
reducer coupling threaded
Trust in these components also stems from rigorous testing procedures that certified producers follow. International standards, including ISO and ASTM, guide the quality assurance processes that validify a component’s reliability. By adopting these standards, manufacturers assure clients of the reducer coupling threaded system’s capability to handle specified loads without failure, thus bolstering trust.
Amidst the myriad benefits, maintenance of these systems cannot be overstated. Regular maintenance checks help detect wear in the threading or any other mechanical stresses before they snowball into significant issues. Proper lubrication is key and involves using the correct type of lubricant to suit the specific material and operating conditions of the reducer. Routine checks not only extend the lifespan of the system but also ensure consistent performance, proving indispensable for industries where downtime equates to financial loss.
Choosing the right reducer coupling threaded system, therefore, requires a discerning eye, informed not only by immediate needs but also by long-term operational goals. Opt for systems that offer easy integration with existing machinery and are backed by comprehensive warranty policies. In selecting the ideal product, industries should consider those that provide training for technicians to ensure correct installation, use, and maintenance. This hands-on knowledge reinforces the importance of correctly executed systems to avoid mishaps and ensure smooth operations.
In conclusion, the journey with reducer coupling threaded systems is one that reflects a blend of intricate engineering prowess and real-world application insights. These components are not just mechanical parts; they are key contributors to an industry’s efficiency and sustainability drive. With careful selection, customization, and adherence to maintenance protocols, businesses can significantly augment their operational efficiency and achieve a sturdy mechanical backbone for their processes.
Post time:
Feb-11-2025