In the realm of industrial mechanics and construction, threaded joints stand as a pinnacle of engineering precision and strength. These specially designed connectors hold together parts in a myriad of applications, ranging from the assembly of machinery to the building of robust pipelines in the most demanding environments. A threaded joint provides the perfect blend of flexibility, strength, and integrity required in modern engineering projects.
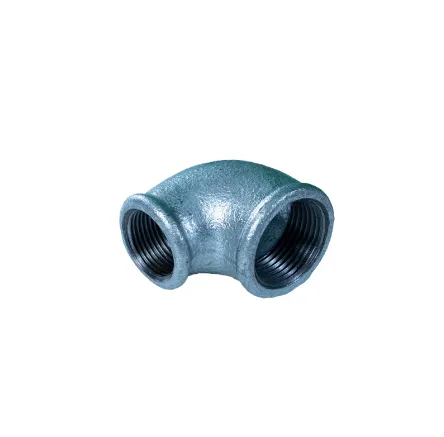
Threaded joints are connections created by the intersection of a male thread and a female thread, providing a strong hold yet allowing for disassembly when necessary. Their versatility makes them an indispensable component in industries such as automotive manufacturing, oil and gas, construction, and even aerospace.
From personal experience as a seasoned engineer, it's clear that selecting the right type of threaded joint is crucial for ensuring safety, durability, and performance. The variety of threaded joints, including standard thread, pipe thread, and fastener thread, each brings specific advantages to different industrial needs. Using these joints extends beyond mere connection purposes; they are vital for maintaining the integrity of the entire assembly under various operational stresses.
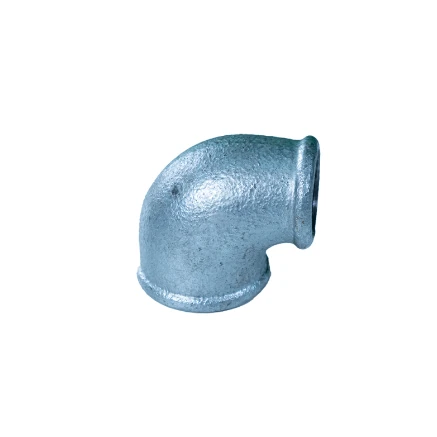
For manufacturers, understanding the different materials in which threaded joints are made can vastly impact the application's success. Most commonly,
threads are carved from durable materials such as stainless steel, titanium, or high-strength polymers. These materials are selected based on their resistance to corrosion, weight requirements, and mechanical demands. For instance, stainless steel threaded joints are often chosen for their excellent resistance to corrosion in harsh environments, making them ideal for outdoor use or chemical processing plants.
A noteworthy aspect of threaded joints is their ease of use combined with superior holding power. Their design enables a firm and stable connection, which is essential for applications where vibration or pressure changes frequently occur. Threaded joints can effectively distribute stress over a larger area, significantly reducing the risk of fastener failure.
threaded joint
To enhance the expertise surrounding threaded joints, exploring the technological advancements in thread engineering is essential. Digital tools and software now allow for precision design and testing of threaded joints, ensuring optimal performance even before they are physically implemented. This advancement not only saves time but significantly reduces the cost related to testing and potential downtimes caused by mechanical failures.
In terms of authoritativeness, it's important to note that engineering standards such as those from the American Society of Mechanical Engineers (ASME) set stringent criteria for the design, testing, and application of threaded joints. Adherence to these standards is non-negotiable for ensuring safety and performance, highlighting the essential role of compliance in threaded joint selection and use.
Trustworthiness of threaded joints comes from their long history of reliable performance across countless applications. Companies that prioritize regular inspections and maintenance bolster the dependability of threaded joints. Proper lubrication and regular torque checks are fundamental practices that prevent wear and ensure joints remain secure and efficient over time.
Design innovations also see the introduction of self-locking nuts and anti-corrosive coatings to further enhance the lifespan and reliability of threaded joints. These advancements provide peace of mind and ensure that threaded joints remain a trusted choice for engineers worldwide.
In conclusion, threaded joints are more than mere components; they are the backbone of countless structures and machines. The reliability and flexibility they offer ensure they remain a mainstay in industrial applications. Both new developments in their design and adherence to rigorous standards confirm their essential role in upholding the structural integrity and operational success of engineering projects globally.
Post time:
Feb-15-2025