Galvanized caps serve as a pivotal component in many industrial and residential applications. These essential elements are used extensively in pipe systems, tanks, and a variety of other frameworks that require robust sealing and protection against environmental factors. The importance of choosing the right type of galvanized cap cannot be understated, as their quality directly influences the durability and safety of the entire system they are part of.
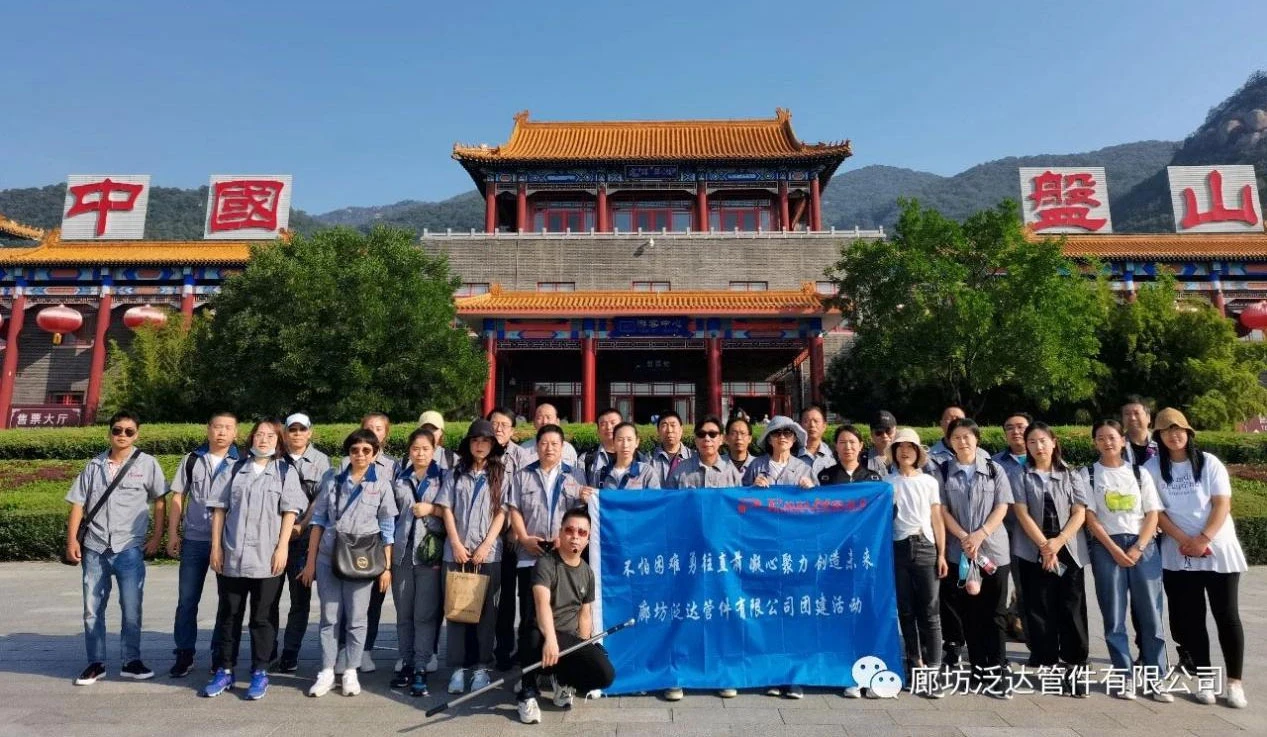
One of the vital features of galvanized caps is their ability to resist corrosion. The galvanization process involves coating the cap with a layer of zinc, which serves as a sacrificial anode. This protection method is particularly beneficial in environments where moisture and other corrosive elements are prevalent. Over time, exposure to such conditions can lead to rust and deterioration of metal components that aren't adequately protected, highlighting the necessity of high-quality galvanized caps.
Real-world experience shows that choosing the correct fitting is not just about selecting a cap that fits but involves considering various other factors. Experts in the plumbing and construction industries emphasize the significance of ensuring that the chosen cap is compatible with the specific material and structural demands of the project. It's essential to verify that the cap adheres to the established industry standards to guarantee both performance and safety.
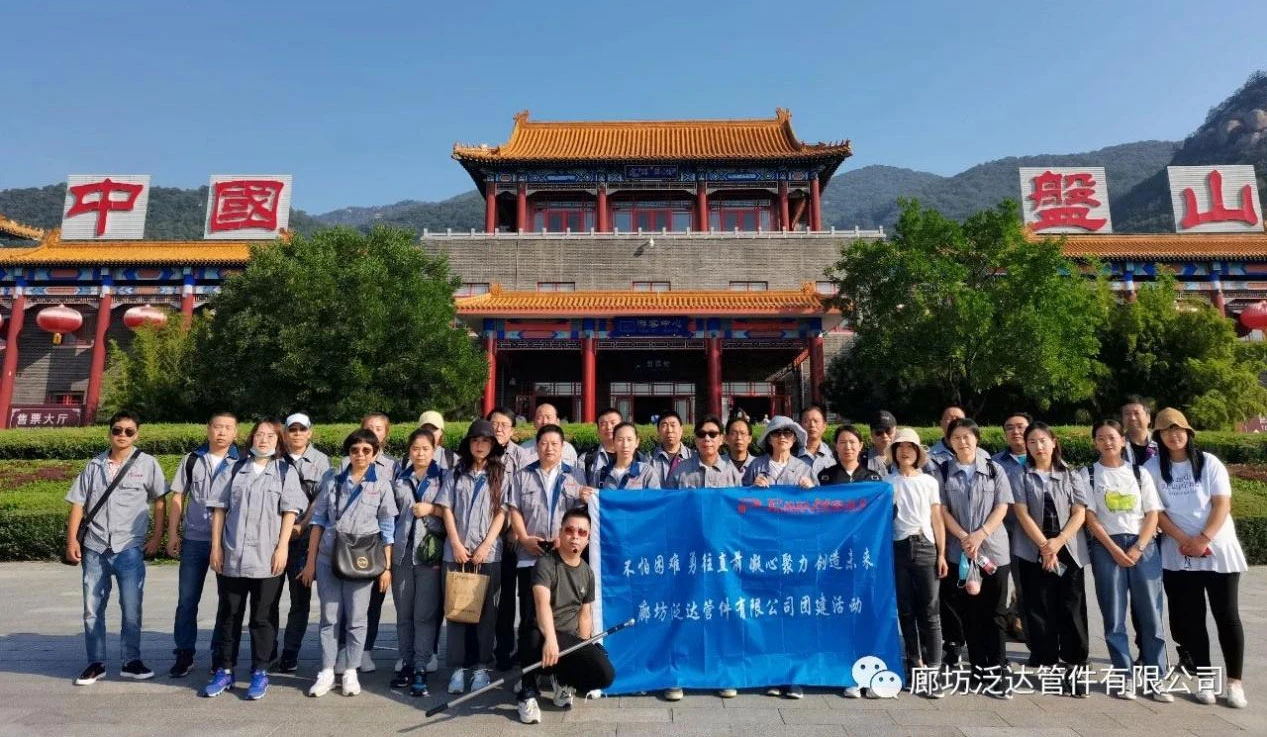
Technological advancements in manufacturing have resulted in galvanized caps that are not only durable but also designed to withstand higher pressure and more extreme temperatures than ever before. This progress aids industry professionals in implementing solutions that ensure longevity and reliability in their applications. Experienced engineers stress the importance of consulting with manufacturers and technical experts when selecting galvanized caps for high-stakes projects.
From an authoritative perspective, regulatory bodies and quality assurance organizations advocate for stringent testing and certification processes. This practice ensures that galvanized caps meet safety standards and perform as expected. It's important for consumers to seek products that carry recognized certifications, as these indicators provide confidence in the product’s quality and effectiveness.
1 galvanized cap
Trustworthiness in the selection of galvanized caps also lies in the transparency and reputation of the supplier. Working with reputable manufacturers who provide comprehensive documentation and clear communication about the production processes and materials used can make a significant difference. Buyers are encouraged to review supplier history, customer testimonials, and industry reputation to gauge reliability.
Case studies and user testimonials often illustrate the performance of galvanized caps under various conditions. Such documentation provides insight into their practicality across multiple scenarios—from subterranean plumbing networks to outdoor construction projects. Users consistently report that the use of reliable galvanized caps significantly curtails maintenance needs and prolongs the lifecycle of the equipment they protect.
Finally, sustainable practices in the production and recycling of galvanized caps are becoming more prevalent. Consumers and professionals alike are increasingly prioritizing environmentally responsible products. Manufacturers committed to sustainability employ processes that minimize waste and reduce the carbon footprint of their products, offering an added layer of confidence to environmentally-conscious buyers.
In conclusion, the choice of a galvanized cap goes beyond mere compatibility and extends into considerations around durability, proven performance, certification, supplier reliability, and environmental responsibility. By focusing on these factors, individuals and companies can enhance the effectiveness and longevity of their systems, making galvanized caps an indispensable element in any construction or maintenance toolkit.
Post time:
Feb-01-2025