Galvanized pipe caps play a crucial role in the longevity and efficiency of a variety of piping systems. They are often used to cover the ends of a pipe to keep out dirt, debris, and other materials that might compromise the system's performance. With their protective zinc coating, galvanized pipe caps are a preferred choice in many industrial, commercial, and residential applications, particularly where corrosion resistance is necessary.
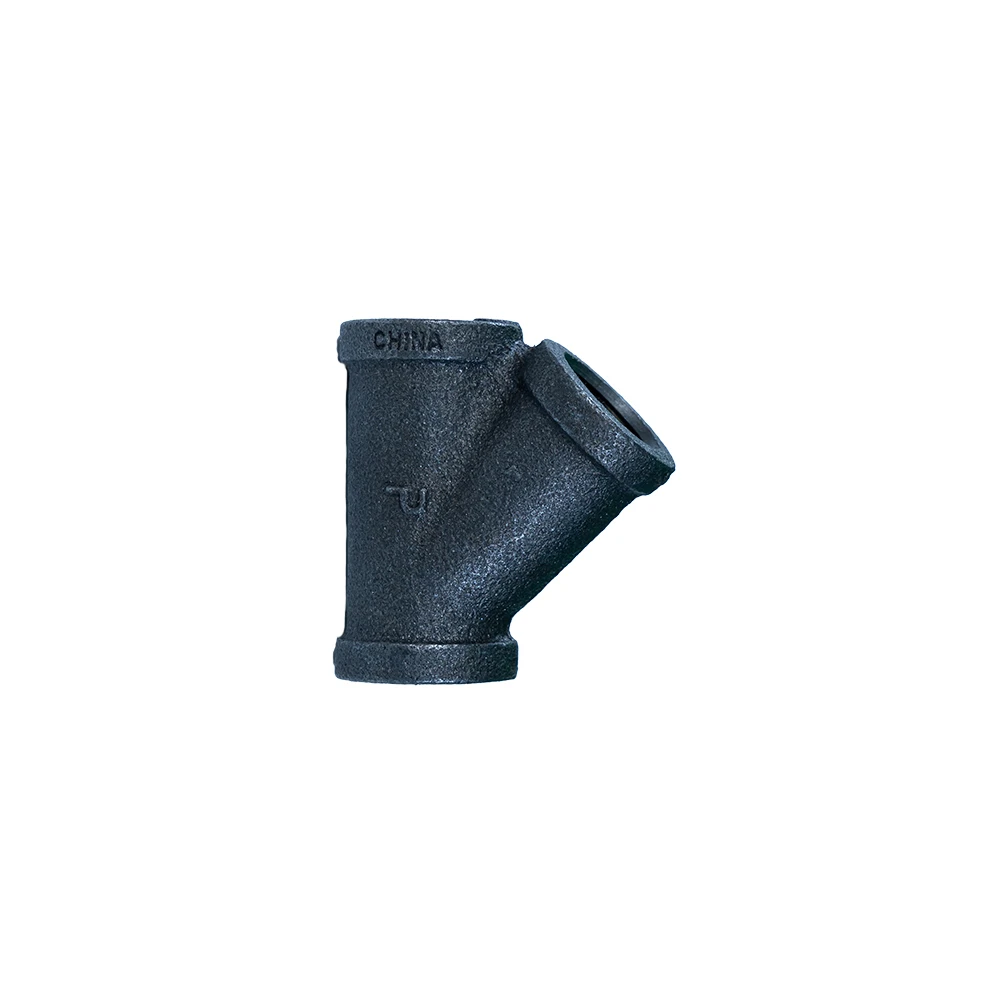
The advantage of using galvanized pipe caps over non-galvanized options is well-anchored in their superior resistance to rust and corrosion. This is achieved through the process of galvanization, which involves applying a protective layer of zinc to the metal surface. The zinc serves as a sacrificial anode, meaning it will corrode before the metal underneath does, thus prolonging the life of the pipe system it protects. This benefit is pronounced in environments where exposure to moisture and changes in weather are frequent, such as in outdoor installations.
From my extensive experience working in the industrial piping sector, I have observed that investing in galvanized pipe caps significantly reduces maintenance costs over the years. For instance, I worked with a manufacturing facility that primarily used galvanized pipe fittings throughout their operational framework. Their initial investment in galvanized materials paid off massively by virtually eliminating the need for frequent replacements and repairs due to rust, compared to an earlier alternate setup that used standard steel pipe caps.
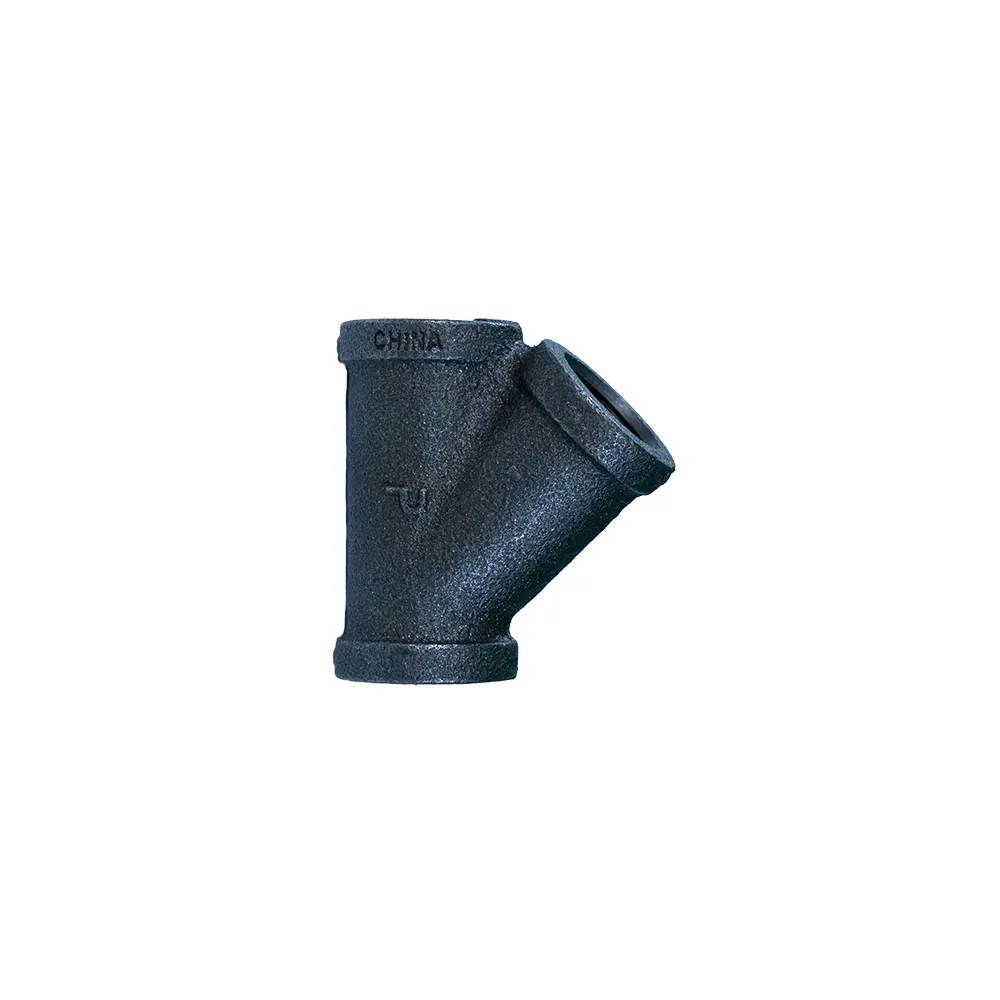
Galvanized pipe caps are not just confined to industrial use; their application extends seamlessly into residential settings, especially in plumbing systems. Homeowners appreciate these caps for their durability and the peace of mind they provide. Moreover, these caps add an extra layer of safety by protecting the piping system from unnecessary leakage—another testimony to their effectiveness based on real-world applications.
galvanized pipe cap
When selecting a galvanized pipe cap, one must consider specific expertise factors like size and compatibility with the piping system. Precision is key—choosing the right size ensures a proper fit, which is paramount in maintaining the integrity of the seal. Pipe caps are available in various sizes and specifications, and selecting the wrong one could lead to performance issues, including misalignment and subsequent leaks.
Trustworthiness in sourcing is another critical factor. The quality of galvanized pipe caps can vary considerably between manufacturers. Therefore, it's crucial to rely on established brands or vendors known for their manufacturing expertise and adherence to industry standards. A trustworthy manufacturer will typically provide certifications like ISO ratings, ensuring the product has been inspected and meets all necessary quality criteria.
Authoritative resources suggest that looking beyond the price tag and focusing on the demonstrated lifespan and performance history of these fittings plays a more significant role in decision-making. For instance, authoritative guides recommend the involvement of an experienced plumbing or industrial engineer during the selection process for industrial systems—this ensures that all variable factors, including pressure ratings and environmental conditions, are duly considered.
In conclusion, galvanized pipe caps represent a blend of expert engineering and reliable protection for piping systems. Their benefits are clearly documented in industry records and practical applications, providing not just theoretical but tested solutions. Their role in enhancing the efficiency, safety, and longevity of piping systems across applications makes them a stalwart choice for any setting requiring robust and resilient piping solutions.
Post time:
Jan-21-2025